Optimización de cemento Portland con caliza
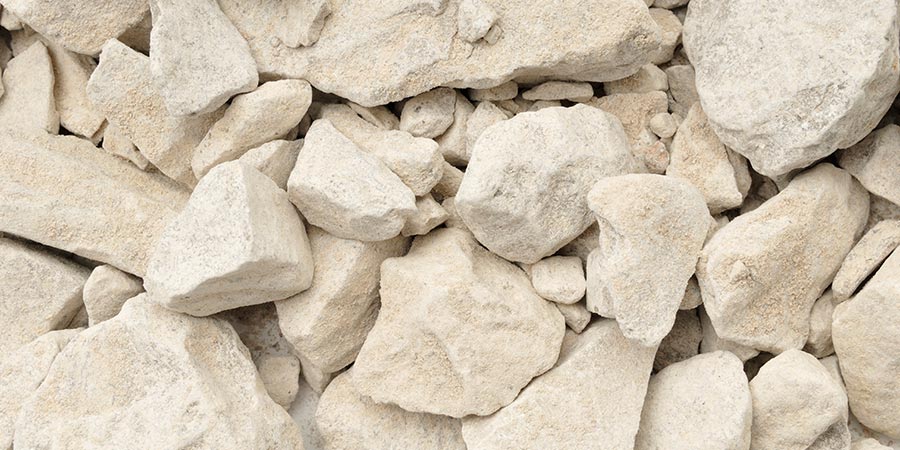
El cemento Portland con caliza ofrece ventajas en el rendimiento y control de las resistencias en cemento y en concreto, además de reducir los costos de la producción y las emisiones de CO2. Sin embargo, es importante utilizar el aditivo de cemento adecuado con la adición adecuada de caliza para lograr estos beneficios.
Considerar los siguientes factores cuando se produzca cemento Portland con caliza.
- Existen normas de cumplimiento y códigos de práctica a seguir cuando se utilizan materiales cementantes suplementarios como la caliza. Por ejemplo, en la norma Europea EN 197-1, la caliza debe cumplir con criterios específicos para su pureza de CaCO3 (>75%), tener un contenido limitado de arcilla (< 1.20 g/100 g basado en pruebas con azul de metileno), además de tener un carbonato orgánico total que no supere el 0.20% en masa para los cementos LL y el 0.50% para los cemento L.
- La presencia de caliza tiene un impacto significativo en el proceso de molienda de cemento. La caliza influye en el Blaine SSA, el aporte de humedad, temperatura interna de molienda, coating, la aglomeración, la retención del molino (llenado de huecos), la eficiencia de molienda del clinker y las características de fluidez del cemento. Esto impacta negativamente la eficiencia de molienda. Cda 1% adicional de caliza, típicamente incrementa el área de superficie específica Blaine (SSA) de 5-8 m2/kg (considerando kWh/t constantes).
- La cantidad de caliza (y su impacto en el proceso de molienda) puede tener un efecto adverso en el rendimiento del cemento. El aumento de caliza generalmente resulta en una distribución de partícula más amplia con un valor de Blaine y residuos más altos. Esto, junto con el factor de clinker más bajo, afecta negativamente el rendimiento del cemento, incluyendo el desarrollo temprano de resistencias, la durabilidad a largo plazo y la fluidez del cemento seco.
Enfoques para mitigar los efectos de la caliza
Reducir la producción del molino para aumentar la figura del cemento puede aliviar algunos de estos desafíos, pero sólo una parte de estos. Hay una reducción de la resistencia del mortero a los 28 días alrededor de 0.75 MPa por cada 1% de incremento de caliza utilizada en un rango mayor al 5%. Una molienda más fina obtenida al reducir la producción del molino aumentará la resistencia en el rango de 1 MPa por cada aumento de 15-20 m2/kg en Blaine SSA (en una pendiente de distribución de tamaño de partícula constante). Esto representa una reducción aproximada del 7-10% en la producción del molino. Dadas estas métricas, es poco probable que una reducción en la producción del molino por sí sola, compense adecuadamente la reducción de resistencia causada por el uso de caliza.
Un enfoque más efectivo es utilizar un aditivo de cemento mejorador de calidad, que puede tener un impacto significativo en las resistencias. Para una ganancia de 5 MPa sería posible aumentar la piedra caliza en aproximadamente un 7% para la misma producción del molino. Dado que la resistencia se reduce sustancialmente en los niveles más altos de caliza (> 5%) es importante la selección adecuada de aditivo para mejorar la calidad. Además, elegir el aditivo adecuado, contrarresta el impacto negativo en la capacidad de flujo, llenado de huecos, el coating y la distribución del tamaño de partícula. Además, este enfoque suele ser más económico y logísticamente atractivo comparado con reducir la salida del molino.
Con base en los hallazgos anteriores, es necesario seguir los siguientes pasos para la producción de cemento Portland con caliza:
- Seleccione las características de desempeño deseadas.
- Decida la producción del molino necesaria con base en la logística y los volúmenes.
- Evalúe las tecnologías de cemento de aditivos.
- Decida la cantidad máxima de caliza capaz de satisfacer los requisitos de rendimiento del cemento.
Tomar en cuenta estos pasos puede traer mejoras sustanciales para la calidad del cemento al tiempo que se reducen los costos de producción y se minimizan las emisiones de CO2.
Tags
- Cement production
- OPTEVA™